Partie 1 : Équipement et pièces de suspension automobile
1. Processus d'usinage des engrenages
Selon différentes exigences structurelles, le principal processus technologique de traitement des pièces d'engrenage est le forgeage des ébauches → la normalisation → l'usinage de finition → la mise en forme des engrenages → le chanfreinage → le taillage → le rasage → (soudage) → le traitement thermique → le meulage → la coupe des mailles.
Les dents ne sont généralement pas usinées après la chauffe, à l'exception des dents principales et secondaires ou des pièces dont le client a besoin pour broyer les dents.
2. Flux de processus d'arbre
Arbre d'entrée : forgeage de la billette → normalisation → usinage de finition → laminage des dents → perçage → façonnage des dents → chanfreinage → taillage → rasage → traitement thermique → meulage → ajustement par maillage.
Arbre de sortie : billette de forgeage → normalisation → usinage de finition → meulage et taillage → rasage → traitement thermique → meulage → garniture d'appariement.
3. Flux de processus spécifique
(1) billette de forgeage
Le forgeage à chaud est un processus de forgeage d'ébauche largement utilisé pour les pièces d'engrenages automobiles. Dans le passé, les ébauches de forgeage à chaud et d'extrusion à froid étaient largement utilisées. Ces dernières années, la technologie de laminage à coins croisés a été largement promue dans le traitement des arbres. Cette technologie est particulièrement adaptée à la réalisation d'ébauches d'arbres étagés complexes. Il a non seulement une haute précision, de petites allocations de post-traitement, mais également une efficacité de production élevée.
(2) Normalisation
Le but de ce procédé est d'obtenir une dureté adaptée à la taille ultérieure des engrenages et de préparer la structure pour le traitement thermique final, de manière à réduire efficacement la déformation due au traitement thermique. La normalisation générale est fortement affectée par le personnel, l'équipement et l'environnement, ce qui rend difficile le contrôle de la vitesse de refroidissement et de l'uniformité de la pièce, ce qui entraîne une grande dispersion de la dureté et une structure métallographique inégale, ce qui affecte directement l'usinage et le traitement thermique final.
(3) Usinage de finition
Afin de répondre aux exigences de positionnement du traitement des engrenages de haute précision, des tours CNC sont utilisés pour la finition des ébauches d'engrenages. Le trou intérieur et la face d'extrémité de positionnement de l'engrenage sont traités en premier, puis le traitement de l'autre face d'extrémité et du diamètre extérieur est effectué simultanément. Il garantit non seulement les exigences de verticalité du trou intérieur et de la face d'extrémité de positionnement, mais garantit également que la dispersion de taille de la production d'ébauches de dents à grande échelle est faible. Ainsi, la précision de l'ébauche d'engrenage est améliorée et la qualité de traitement des engrenages suivants est assurée.
Il existe trois méthodes principales de positionnement et de serrage pour le traitement des pièces d'arbre :
1. Positionnement avec le trou central de la pièce : lors du traitement de l'arbre, la coaxialité de chaque surface extérieure et face d'extrémité de la pièce, ainsi que la verticalité de la face d'extrémité par rapport à l'axe de rotation sont les principaux éléments de leur position mutuelle. précision. La base de conception de ces surfaces est généralement Les deux sont l'axe central de l'arbre. Si deux trous centraux sont utilisés pour le positionnement, cela respecte le principe de la coïncidence de la référence.
2. Le cercle extérieur et le trou central sont utilisés comme référence de positionnement (une pince et un haut): bien que la précision de centrage soit élevée, la rigidité est médiocre, en particulier lors du traitement de pièces plus lourdes, elle n'est pas assez stable et la coupe le montant ne doit pas être trop important. Lors de l'usinage d'ébauche, afin d'améliorer la rigidité de la pièce, la surface extérieure de l'arbre et un trou central peuvent être utilisés comme référence de positionnement pour le traitement. Cette méthode de positionnement peut supporter un grand moment de coupe et est la méthode de positionnement la plus courante pour les pièces d'arbre.
3. Utilisez les deux surfaces circulaires extérieures comme référence de positionnement : Lors de l'usinage du trou intérieur de l'arbre creux (par exemple : usinage du trou intérieur du cône Morse sur la machine-outil), le trou central ne peut pas être utilisé comme référence de positionnement , et les deux surfaces circulaires externes de l'arbre peuvent être utilisées comme référence de positionnement. donnée de positionnement. Lorsque la pièce est la broche de la machine-outil, les deux tourillons de support (référence d'assemblage) sont souvent utilisés comme référence de positionnement, ce qui peut assurer la coaxialité du trou conique par rapport au tourillon de support et éliminer l'erreur causée par le désalignement des données.
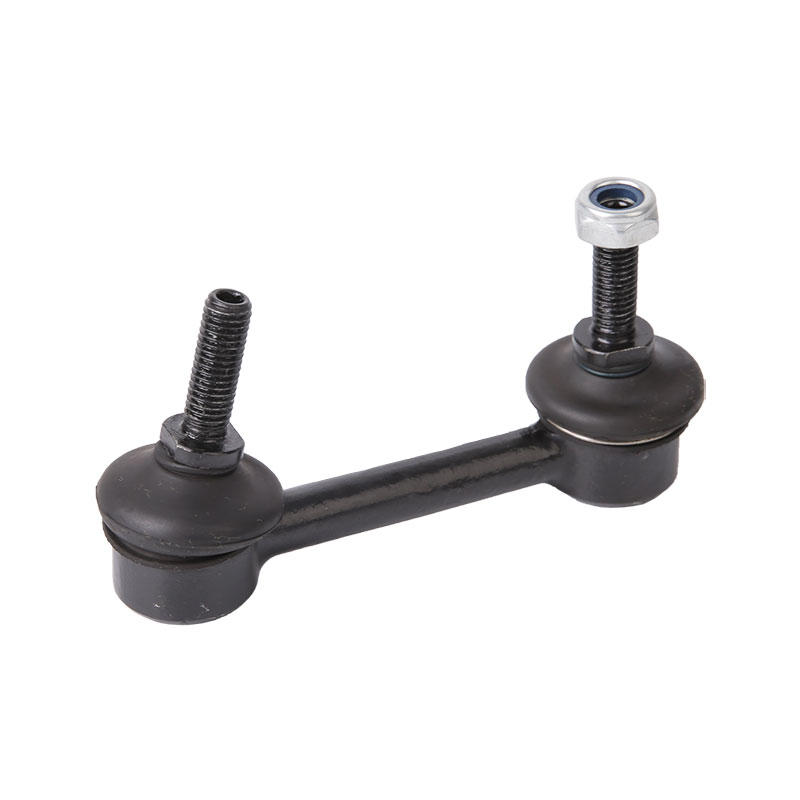
Partie II : Pièces de coque
1. Flux de processus
Le flux de processus général est le fraisage de la surface du joint → les trous de processus d'usinage et les trous de connexion → les trous de roulement à alésage grossier → les trous de roulement à alésage fin et les trous de goupille de positionnement → le nettoyage → la détection des tests de fuite.
2. Méthode de contrôle
(1) Appareils
Le processus d'usinage du carter de transmission est pris comme exemple de "l'usinage du centre d'usinage vertical. Processus 10 # Usinage du centre d'usinage vertical processus 20 # Usinage du centre d'usinage horizontal processus 30 #", trois ensembles de montages de centre d'usinage sont nécessaires pour éviter les pièces Le la déformation de serrage doit également être prise en compte, comme l'interférence de l'outil, le fonctionnement flexible, plusieurs pièces et une pince et la commutation rapide.
(2) Aspect outil
Dans le coût de fabrication des pièces automobiles, le coût de l'outillage représente 3 à 5 % du coût total. L'outil composite à structure modulaire présente les caractéristiques d'une haute précision, d'un porte-outil réutilisable et d'un petit inventaire, et est largement utilisé. Cela peut considérablement raccourcir le temps de traitement et améliorer l'efficacité du travail. Par conséquent, lorsque les exigences de précision ne sont pas élevées et que les outils standard peuvent obtenir de meilleurs résultats de traitement, des outils standard doivent être utilisés autant que possible pour réduire les stocks et améliorer l'interchangeabilité. Dans le même temps, pour les pièces produites en série, l'utilisation d'outils composites avancés non standard pour les pièces nécessitant une grande précision peut améliorer la précision d'usinage et l'efficacité de la production.